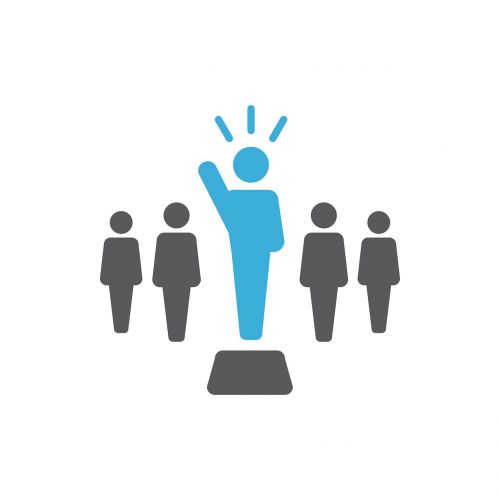
Completing some tasks may not be necessary, specific procedures may need to be repeated more often than necessary, employees may be wasting time on pointless tasks, and materials may be wasted throughout production.
Although you would assume that significant enterprises and organizations are the only places where this kind of operational inefficiency happens. It affects every department of small to medium-sized businesses. Successful businesses focus on efficiency, and you’re about to learn one of the best methods to make your company a process lean.
How can You Apply Lean Process Improvement to Your Company?
- Review the process you want to improve
This phase is crucial since you won’t be able to focus your efforts if you don’t know what you need to work on. You must speak with frontline staff to do it.
The biggest mistakes businesses make during this process is making changes without first discussing the individuals who carry out the work daily. Ask your frontline staff during an interview what aspects of their routine they feel could use improvement.
- Identify what improvements need to be made
It’s time to include your team again after determining what must be changed. Your team likely already knows how to solve the issue but has been unable to due to a “That’s how we’ve always done it” mentality.
- Implement the suggested changes
How will you implement the changes? Make a plan so everyone can understand it and support the process lean. The best approach to guarantee organizational success is to do this.
- Monitor how the changes are impacting your efficiency
While it would be wonderful if your initial try at execution were a success, the truth is that the process will need to be further improved after it is tested in the field. The only way to accomplish this is by continuous evaluation and monitoring. You can address new problems as they arise, make the required adjustments and a better lean leader.
- Identify what activities add value
You will evaluate every stage of this process lean and every element of your workflow. You must assess each action throughout this period to see if it improves or inhibits your process. When a step is considered excessive, it should be taken out, and the process evaluated without it.
- Limit risk
The risk involved in the production and frequent business is inherent. During this period, dangerous tasks or elements of the current process should be identified, eliminated, or made more straightforward. It can entail automating a process or changing how it’s carried out.
- Standardize the process
Keep detailed records of your work as you develop and improve the procedure. It makes it possible for the procedure to be correctly reproduced by other workers or, depending on the particular procedure, by other teams or departments in your company.
- Ensure compliance
Although a company’s entire culture should change to support process lean improvement, your industry or regulatory body may have specific metrics, practices, and benchmarks you must follow. Efficiency may not come at the expense of compliance.
- Improve the customer experience
Consider “the moment of truth” to be the consumer experience. Whatever enhancements you make to production or service must ultimately have a favorable effect on the client.
Lean Process Improvement Techniques
Several strategies have been developed to help with lean process improvement. It’s crucial to select the appropriate technique for your project and organization, just like you would with the equipment. For instance:
Six Sigma
Six Sigma strives to boost internal and external customer satisfaction by standardizing workflow to reduce process variance. The initials DMAIC stand for:
- Define
- Measure
- Analyze
- Improve
- Control
What are the benefits of lean process improvement?
Process lean improvement offers several advantages to businesses that adopt it. They consist of the following:
- Less waste
- Less inventory
- Increased productivity
- Better quality
- Happier customers
- Fewer costs
- More profits
Your bottom line seems to improve if you eliminate redundancy, streamline your operations, and reduce waste. You’ll have happier customers who return and refer you to others if you can get your customers their products quicker and with less difficulty. Your bottom line again rises with more customers. It is also beneficial for making a better lean leader for your company.
Conclusion
It’s time to restate that process lean improvement is a continuous activity. Now you know how crucial it is to a successful, effective company. If you try to change everything about your company overnight, you will surely fail and probably make things worse than they were before.
Recent Comments